
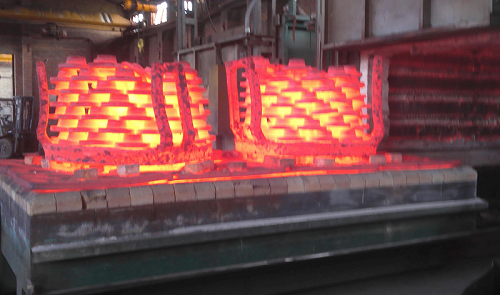
Among all the cast metals, gray cast iron is the most versatile. It has many desirable properties that no other casting alloy possesses, and it is the cheapest iron material that can be effectively utilized. Among iron alloys, gray cast iron has the lowest pouring temperature, which can be verified by its good fluidity and casting ability when pouring complex cavities. Due to its unique solidification mechanism, gray cast iron has very low or even no liquid or solid phase shrinkage, making it easy to obtain qualified castings. Compared with iron alloys of the same tensile strength, gray cast iron has better machinability and vibration damping capacity, higher thermal conductivity, and good corrosion resistance, oxidation resistance, and wear resistance.
2025-08-06 16:53:56
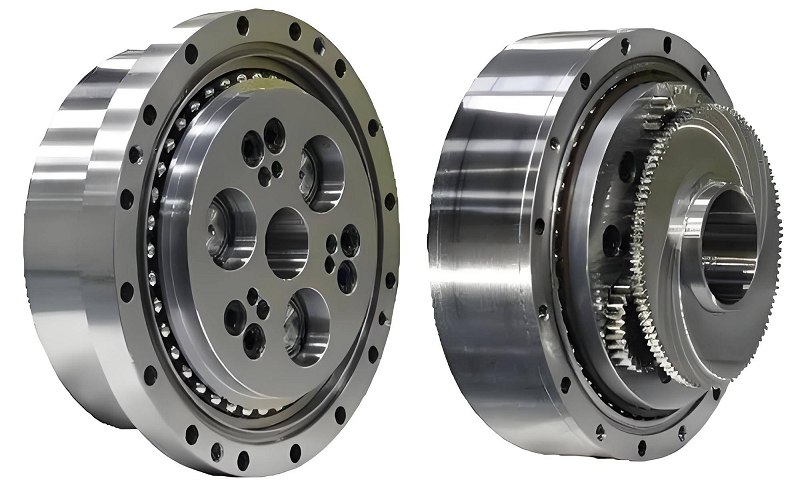
In the fields of automated equipment, industrial robots, and precision machine tools, reducers are like the precise gear hearts, silently transmitting power and precision. Faced with various types of reducers: harmonic, RV, planetary, and cycloidal, how to choose? Who will lead the future? This article analyzes the four major reducer technologies one by one to help you clarify your direction in the selection of technical paths.
2025-08-06 16:49:13
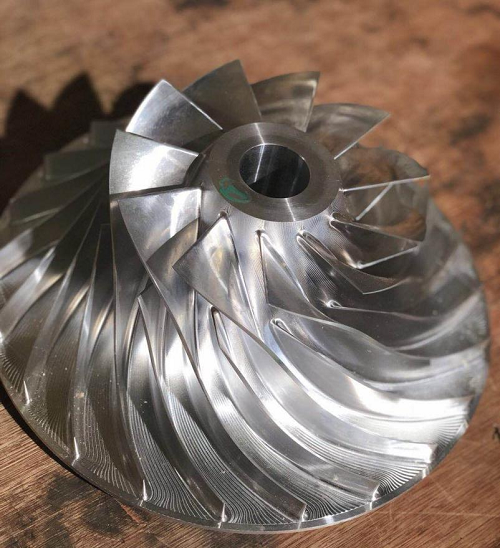
The moving parts of a centrifugal compressor are the key components for achieving gas compression and energy conversion. Their performance directly affects the efficiency, stability and service life of the entire machine. This article will systematically review the main moving parts in a centrifugal compressor and their functions.
2025-08-01 18:27:39
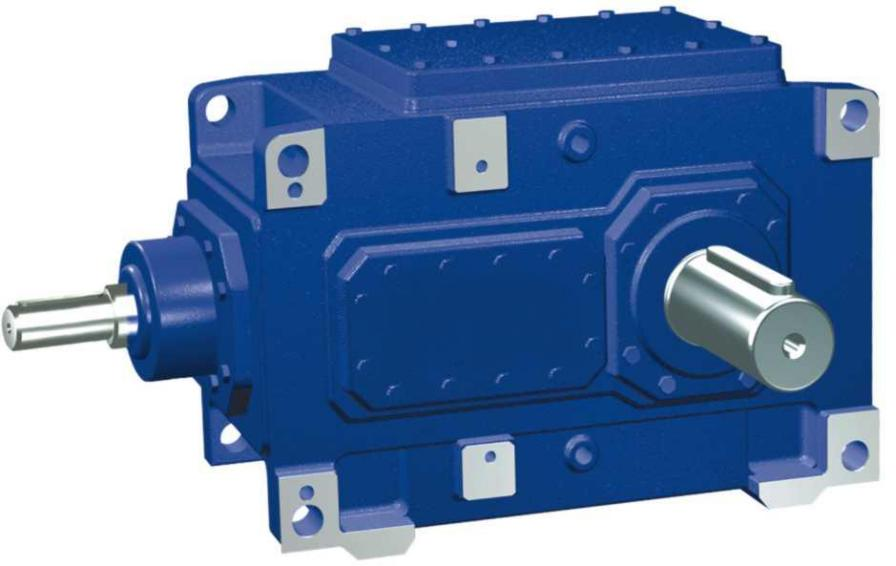
Strategic Partnership and Long-Term Agreements: Establish long-term strategic partnerships with key suppliers (such as steel, bearings, seals, cutting tools, etc.) to secure more favorable prices and more stable supplies.
Introduce Competition and Price Comparison: For non-strategic materials or standard parts, maintain 2-3 qualified suppliers to promote healthy competition.
Joint Purchasing/ Centralized Purchasing: If multiple departments within the company require the same type of materials, centralized purchasing should be carried out to enhance bargaining power.
Local Purchasing: Under the premise of ensuring quality and delivery time, give priority to local suppliers to reduce logistics costs and risks.
2025-07-31 00:00:00
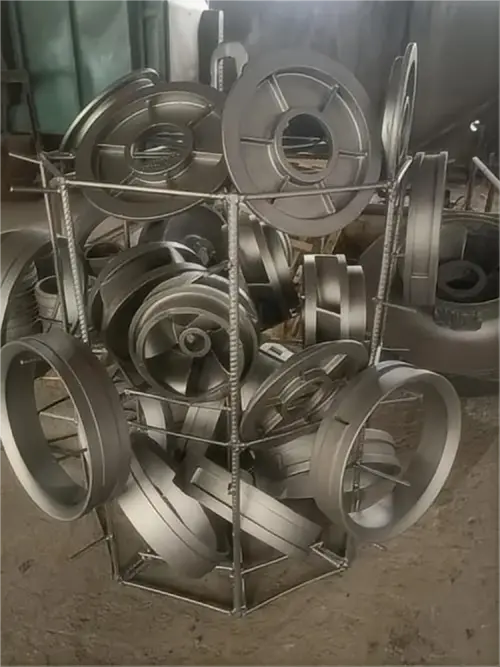
K418 (international designation IN713C) is a nickel-based precipitation-hardened equiaxed grain cast superalloy specifically designed for high-stress and corrosive environments below 900°C. As a core material for China's aero-engine and energy equipment, it achieves a balance among high-temperature strength, thermal fatigue resistance, and environmental tolerance through γ' phase strengthening and high-chromium corrosion resistance design. It is particularly suitable for environments containing corrosive media such as sulfur and chlorine. This report systematically analyzes the composition design principles, performance advantages, manufacturing techniques, and future challenges of K418 alloy.
2025-07-30 16:09:17
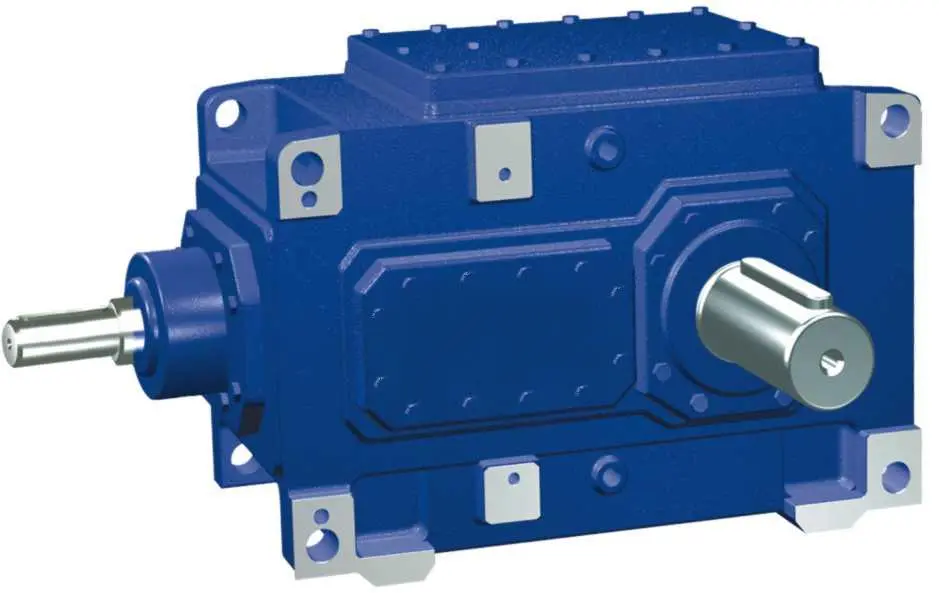
Reducing the manufacturing cost of gearboxes is a systematic project that requires optimization from multiple aspects such as design, materials, processes, procurement, production management, and supply chain. The following are some key strategies and specific methods:
2025-07-30 16:06:38
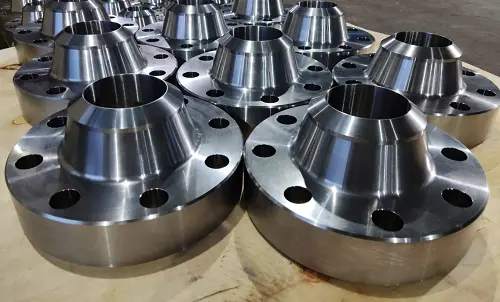
904L steel is a high-grade austenitic stainless steel. Its unique composition provides outstanding performance and durability, making it an ideal choice for applications in the chemical, marine, and other demanding environments.
2025-07-30 13:27:32
Ductile iron castings play a crucial role in the mechanical manufacturing field due to their high strength and good toughness. However, casting defects are like "roadblocks" on the quality journey, causing many casting managers a great deal of trouble.
However, you might not expect that the root causes of the seven common types of defects in ductile iron casting production are all closely related to the selection and use of spheroidizing agents. Understanding the intrinsic connection between spheroidizing agents and defects is the key to improving casting quality and reducing scrap rates.
2025-07-30 13:24:19
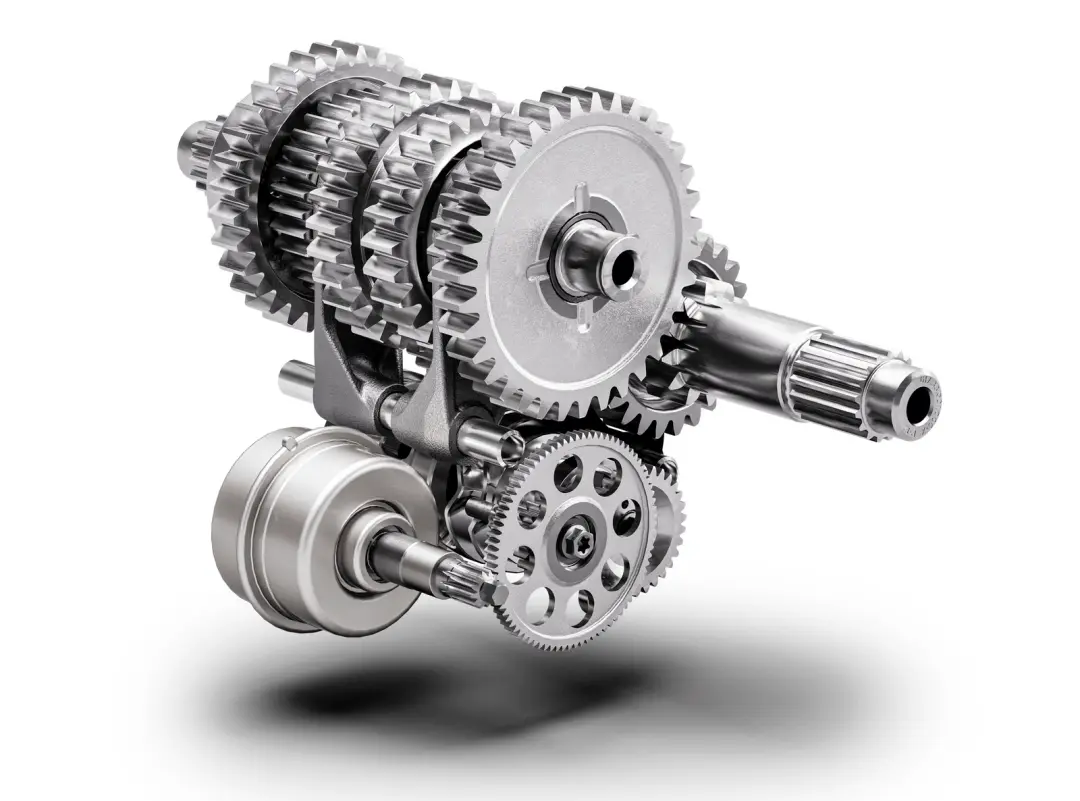
440C alloy, also known as stainless steel alloy 440C, is a high-carbon martensitic stainless steel that offers excellent hardness and wear resistance. This alloy is also known by other names such as X105CrMo17 or 1.4125 and is widely used in the automotive industry due to its outstanding performance. We will explore the various applications and advantages of 440C alloy in the automotive field.
2025-07-24 15:07:09
42CrMo4 (equivalent to the national standard 42CrMo) is a commonly used medium carbon alloy structural steel, featuring high strength, good toughness and hardenability. It is widely used in manufacturing important components such as shafts, gears and connecting rods. Its typical heat treatment process is as follows:
2025-07-24 15:05:38
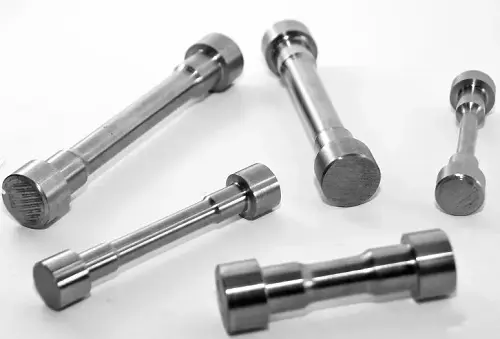
So the question arises: since there are already indicators for judging the plasticity of materials, why go to the trouble of creating a "reduction of area"? It's like, if Zhu Di had already intended in his heart to let Zhu Gaoxu inherit the throne, why did he appoint Zhu Gaochi as the crown prince? Was he just bored or was there some hidden reason?
2025-07-23 16:02:58
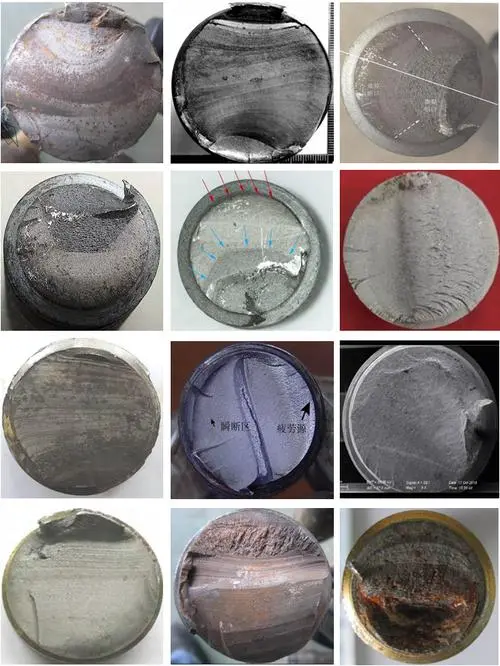
In the field of mechanical engineering, metal fatigue is like a "chronic disease" in the material world - parts gradually develop cracks under repeated stress and eventually break suddenly. This kind of failure often occurs when the material seems intact, so improving fatigue strength is crucial for ensuring engineering safety.
2025-07-23 15:55:21
302