
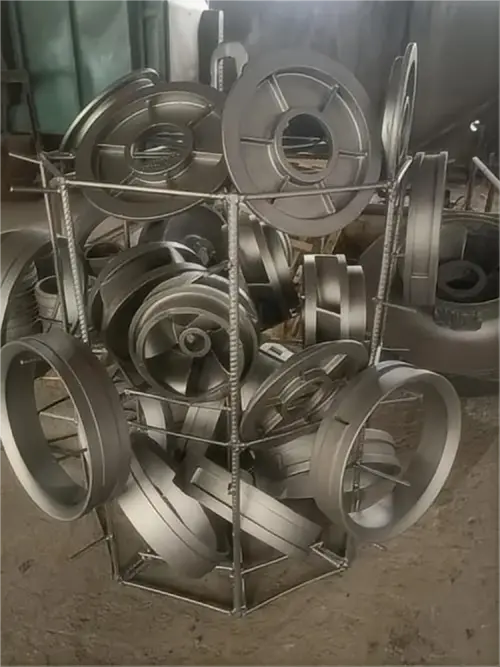
K418 (international designation IN713C) is a nickel-based precipitation-hardened equiaxed grain cast superalloy specifically designed for high-stress and corrosive environments below 900°C. As a core material for China's aero-engine and energy equipment, it achieves a balance among high-temperature strength, thermal fatigue resistance, and environmental tolerance through γ' phase strengthening and high-chromium corrosion resistance design. It is particularly suitable for environments containing corrosive media such as sulfur and chlorine. This report systematically analyzes the composition design principles, performance advantages, manufacturing techniques, and future challenges of K418 alloy.
2025-07-30 16:09:17
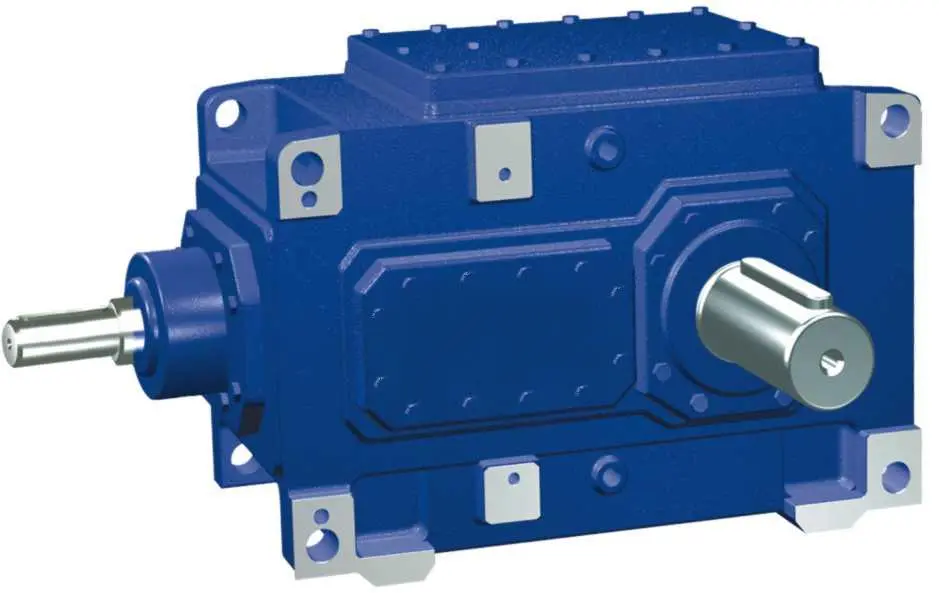
Reducing the manufacturing cost of gearboxes is a systematic project that requires optimization from multiple aspects such as design, materials, processes, procurement, production management, and supply chain. The following are some key strategies and specific methods:
2025-07-30 16:06:38
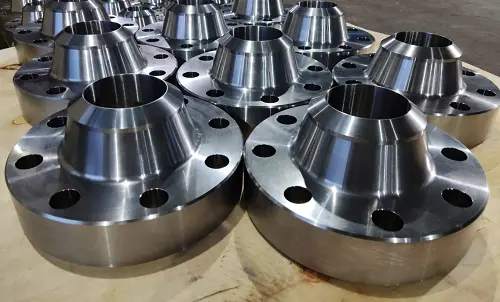
904L steel is a high-grade austenitic stainless steel. Its unique composition provides outstanding performance and durability, making it an ideal choice for applications in the chemical, marine, and other demanding environments.
2025-07-30 13:27:32
Ductile iron castings play a crucial role in the mechanical manufacturing field due to their high strength and good toughness. However, casting defects are like "roadblocks" on the quality journey, causing many casting managers a great deal of trouble.
However, you might not expect that the root causes of the seven common types of defects in ductile iron casting production are all closely related to the selection and use of spheroidizing agents. Understanding the intrinsic connection between spheroidizing agents and defects is the key to improving casting quality and reducing scrap rates.
2025-07-30 13:24:19
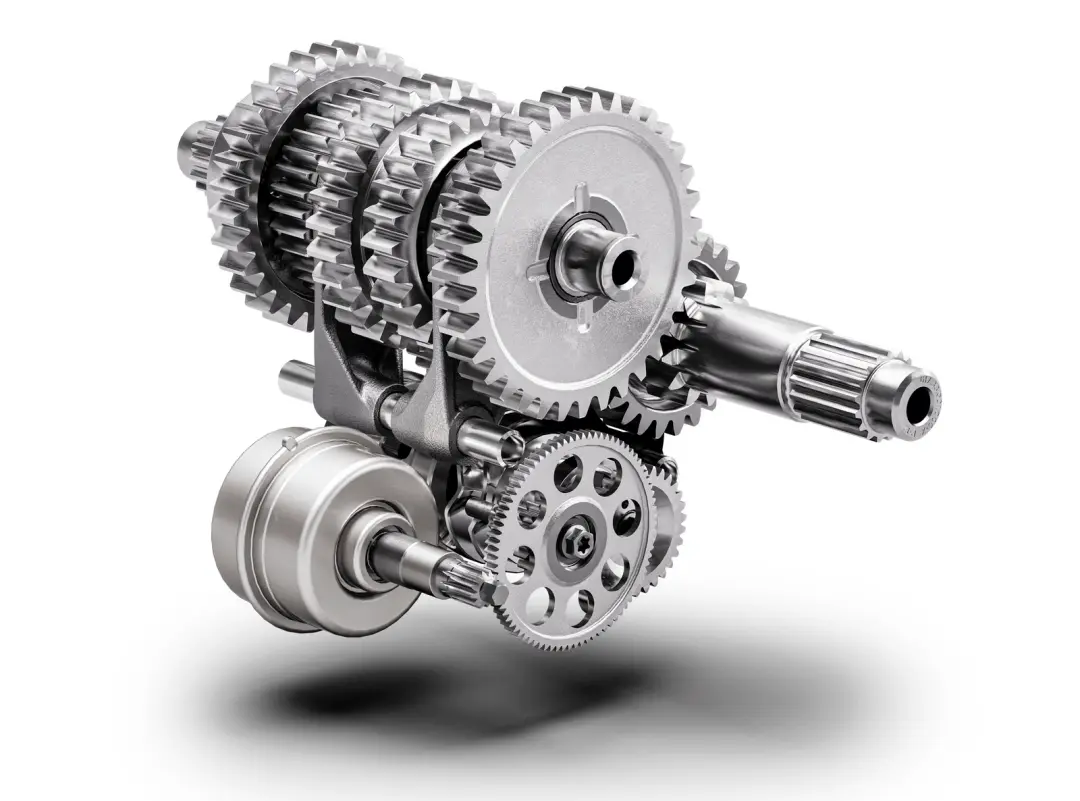
440C alloy, also known as stainless steel alloy 440C, is a high-carbon martensitic stainless steel that offers excellent hardness and wear resistance. This alloy is also known by other names such as X105CrMo17 or 1.4125 and is widely used in the automotive industry due to its outstanding performance. We will explore the various applications and advantages of 440C alloy in the automotive field.
2025-07-24 15:07:09
42CrMo4 (equivalent to the national standard 42CrMo) is a commonly used medium carbon alloy structural steel, featuring high strength, good toughness and hardenability. It is widely used in manufacturing important components such as shafts, gears and connecting rods. Its typical heat treatment process is as follows:
2025-07-24 15:05:38
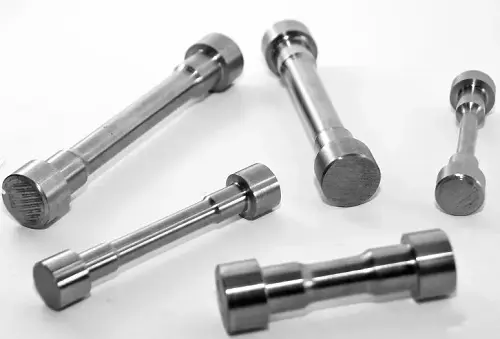
So the question arises: since there are already indicators for judging the plasticity of materials, why go to the trouble of creating a "reduction of area"? It's like, if Zhu Di had already intended in his heart to let Zhu Gaoxu inherit the throne, why did he appoint Zhu Gaochi as the crown prince? Was he just bored or was there some hidden reason?
2025-07-23 16:02:58
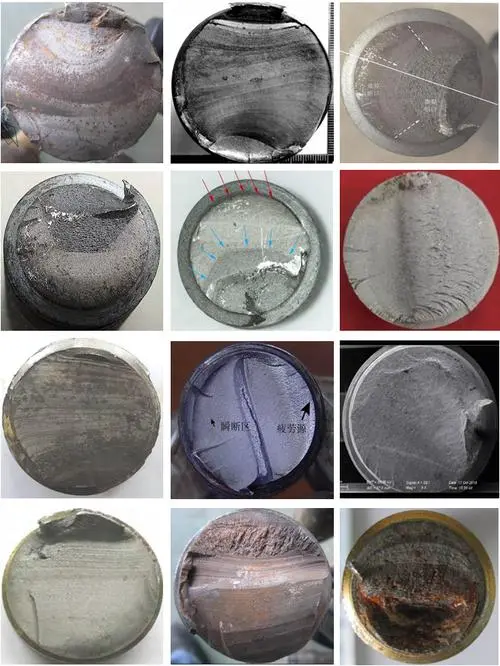
In the field of mechanical engineering, metal fatigue is like a "chronic disease" in the material world - parts gradually develop cracks under repeated stress and eventually break suddenly. This kind of failure often occurs when the material seems intact, so improving fatigue strength is crucial for ensuring engineering safety.
2025-07-23 15:55:21
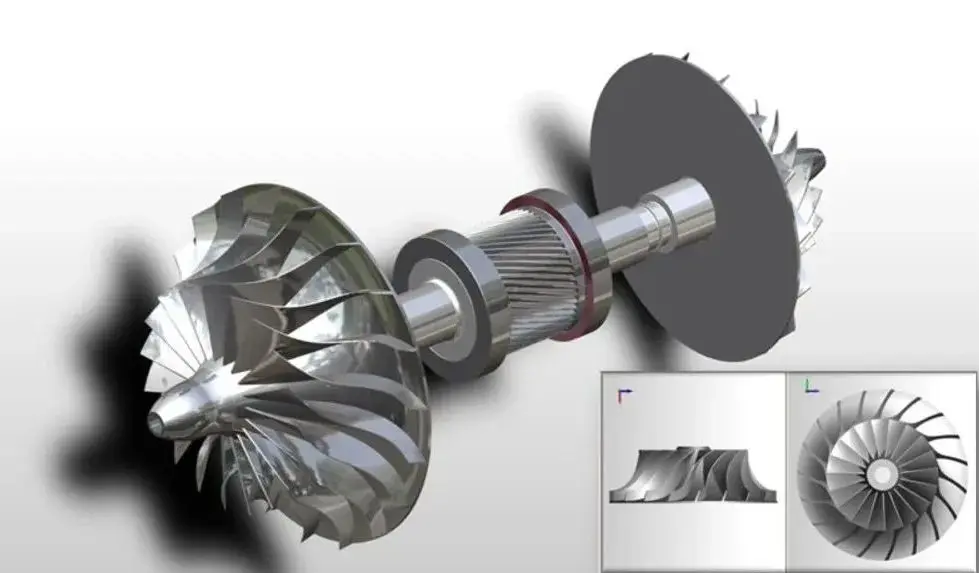
The impeller of a centrifugal compressor plays a core role in its structure, and the material selection of the impeller directly affects the performance, lifespan and applicable working conditions of the equipment. The impeller is installed on the horizontal pinion shaft inside the gearbox. In the figure below, each end of the pinion shaft is equipped with an impeller, which is a common configuration. However, it is equally common to have only one impeller installed on each pinion shaft.
2025-07-22 16:25:38
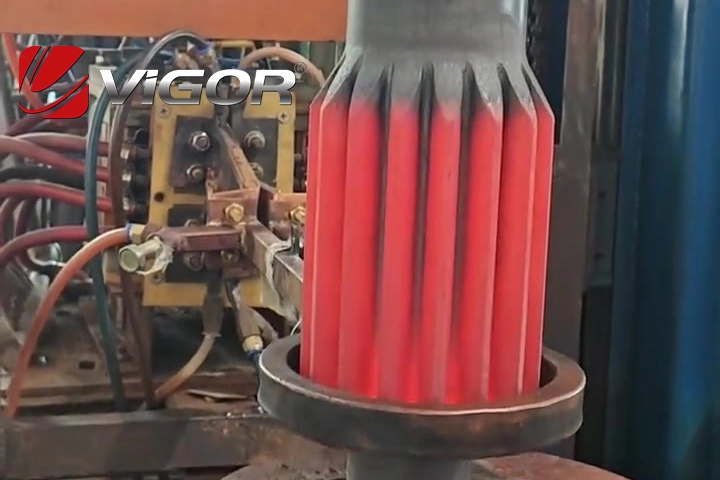
Surface treatment is a process method that artificially forms a surface layer with mechanical, physical and chemical properties different from those of the base material on the surface of the base material. The purpose of surface treatment is to meet the requirements of corrosion resistance, wear resistance, decoration or other special functions of the product. For metal castings, surface heat treatment of lead screws and guide rails is a commonly used surface treatment method.
2025-07-22 16:20:05
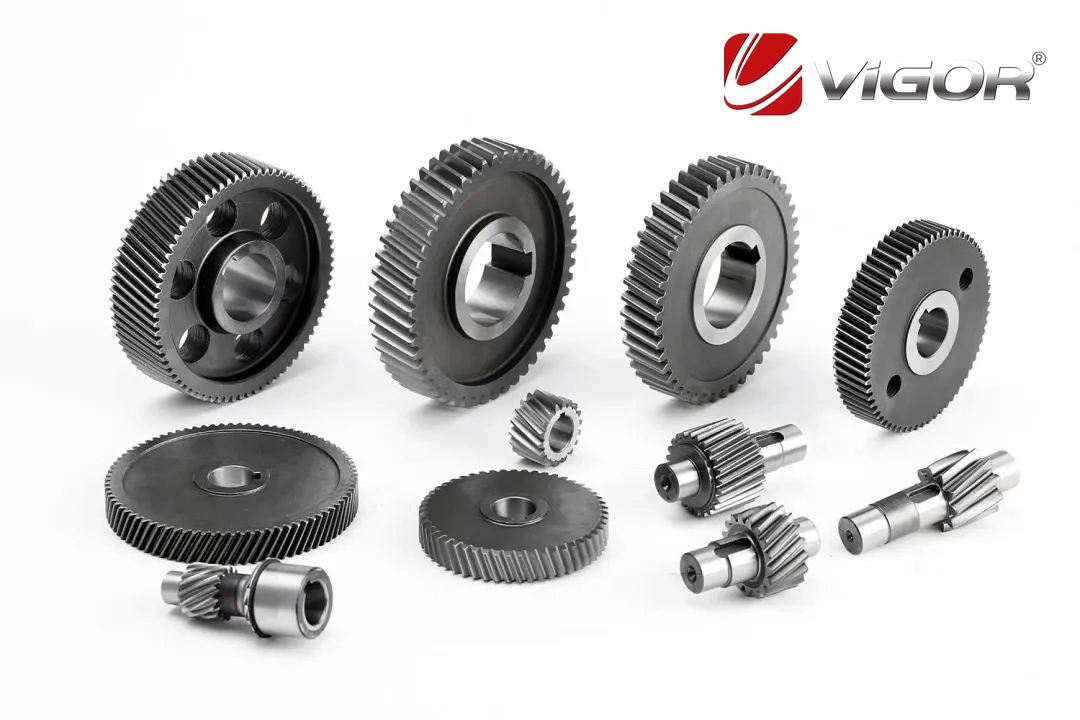
The main technical classifications of gear manufacturing processes can be divided into the following categories:
2025-07-17 17:00:12
In some cases, the corrosion resistance of stainless steel depends on the material series it belongs to. But generally speaking, the key lies in the content of the alloying element molybdenum. A rule of thumb is that the higher the molybdenum content, the stronger the corrosion resistance of the material. Molybdenum can also enhance the material's strength at high temperatures. Let's explore many commonly used stainless steel grades and determine their corrosion resistance levels based on the presence of molybdenum.
2025-07-17 16:50:01
286