
To reduce the porosity of ductile iron through mold design, the following aspects can be considered and optimized
2025-03-27 18:01:59
The production of cast steel parts used to commonly employ water glass self-hardening sand, furan resin self-hardening sand and alkaline phenolic resin self-hardening sand for molding and core making.
2025-03-27 17:58:07
Heat treatment is a crucial step in ensuring the mechanical properties of cast steel parts. Through forming, pouring, shakeout and cleaning, the casting takes its final shape - but it may not be strong or flexible enough for final use. By heating and cooling the metal at different rates, foundries can alter its mechanical properties. But how does the application of heat change the strength or flexibility of the metal?
2025-03-27 17:56:33
Surface treatment is a process method that artificially forms a surface layer with mechanical, physical and chemical properties different from those of the base material on the surface of the base material. The purpose of surface treatment is to meet the requirements of corrosion resistance, wear resistance, decoration or other special functions of the product. For metal castings, the surface treatment methods we commonly use are mechanical grinding, chemical treatment, surface heat treatment, and surface spraying, etc.
2025-03-27 17:55:28
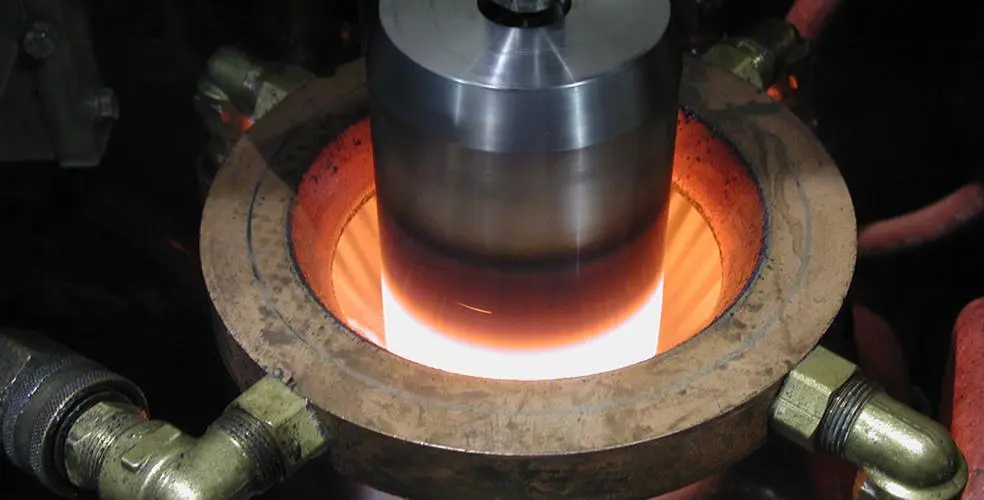
The influence of high-frequency quenching on the internal structure of metals is multi-faceted, specifically manifested in the following aspects:
2025-03-27 17:53:51
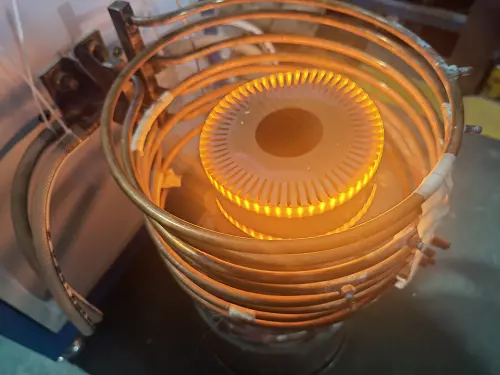
To reduce and eliminate the impact of high-frequency quenching on the internal structure of metals, the following aspects can be considered:
2025-03-27 17:52:11
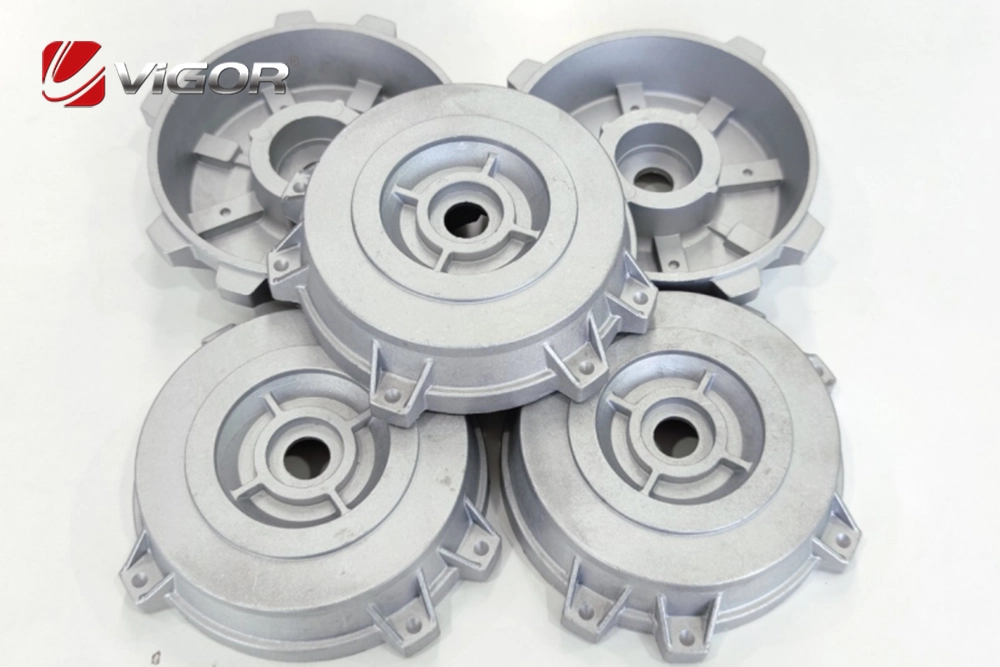
The commonly used materials in die-casting processes mainly include non-ferrous metals such as aluminum, zinc, magnesium, and copper, as well as their alloys. These materials hold significant importance in the die-casting field due to their unique physical and chemical properties.
2025-03-26 13:24:55
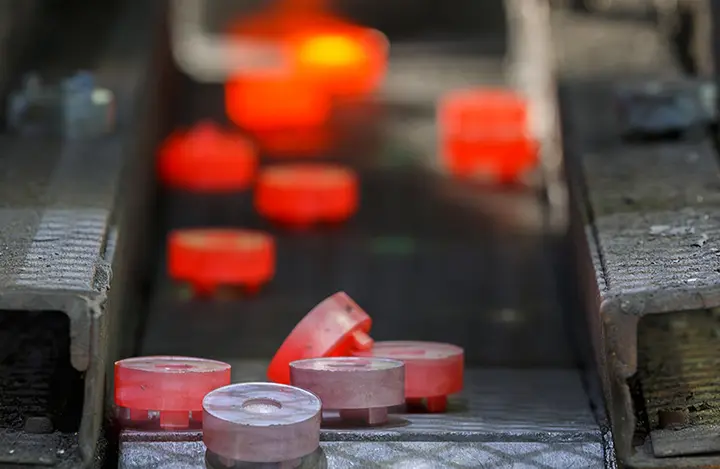
Heat treatment methods have a direct and significant impact on the recrystallization process of metallic materials. Recrystallization is an important process in which metallic materials, during heat treatment, eliminate dislocations and crystal defects generated during cold or hot working through the re-nucleation and growth of grains, thereby restoring the material's plasticity and toughness. The following are several common heat treatment methods and their specific effects on the recrystallization process of metallic materials:
2025-03-26 13:17:21
_1742966068596.webp)
The core of the chemical reaction formation: During the smelting of the molten iron and the subsequent processing, the magnesium, rare earth and other elements in the spheroidizing agent will undergo chemical reactions with sulfur, oxygen and other elements in the molten iron, generating sulfides and oxides. These compounds, such as MgS, MgO, RE2O3, etc., are initially small in size and serve as substrates for the nucleation of graphite, that is, the spheroidization core.
2025-03-26 13:15:24
The strength of resin sand is often classified into room temperature strength and high-temperature strength. Room temperature strength is further divided into initial strength and final strength. Initial strength refers to the strength of the molding sand immediately after mixing, while final strength refers to the strength of the molding sand after 24 hours.
2025-03-26 11:23:15
Carbon
Atomic number: 6
Density (20°C): 2.3 g/cm³
Atomic weight: 12.01
Melting point: > 3550°C (6422°F)
Boiling point: 4827°C (8721°F)
2025-03-26 11:21:16
To determine whether ductile iron is prone to porosity, the following aspects can be considered:
2025-03-25 18:06:59
302