
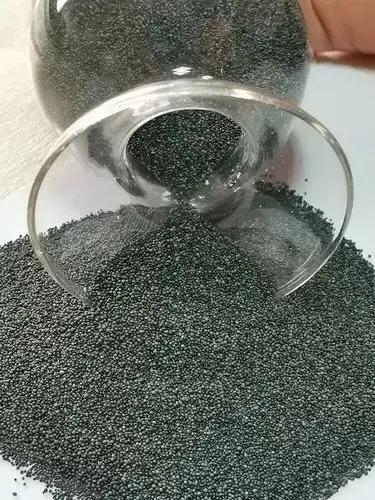
Baozhu sand is a green and environmentally friendly casting sand, also known as electrically fused ceramsite, ceramsite sand, or jewelry sand. Its scientific name is "fused ceramic sand".
Raw Materials and Manufacturing Process
Baozhu sand is made from high-quality bauxite as the raw material and processed through calcination, electric melting, granulation, and screening to produce spherical refractory material particles.
2025-03-25 18:06:03
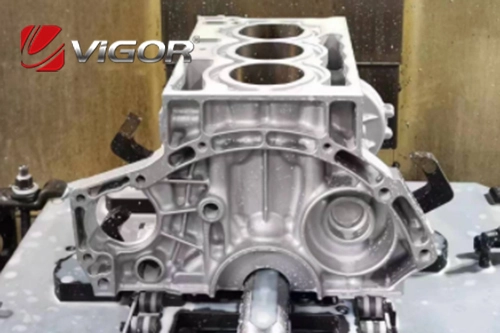
Hot chamber die casting is a time-honored die casting technique characterized by the direct immersion of the injection mechanism into the molten metal. This process is suitable for low-melting-point metals such as zinc, tin, and lead alloys.
2025-03-21 18:09:08
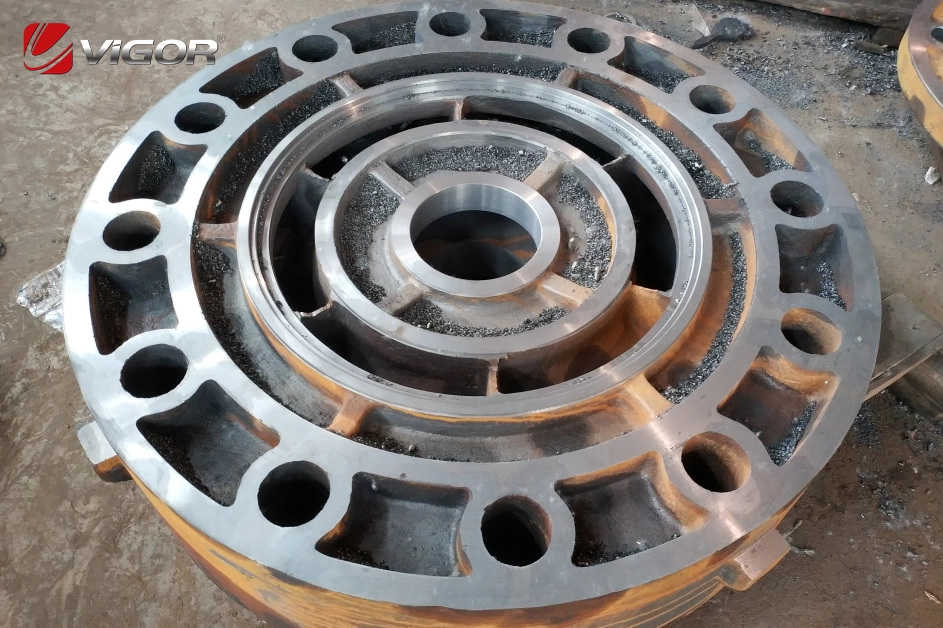
The type, properties, and moisture content of the resin can have an impact. For instance, furan resin with a relatively high moisture content will inhibit the condensation reaction, slow down the hardening speed, and extend the working life and molding time. If the pH value of the resin is too high, it will consume more curing agent, also causing the hardening process to slow down.
2025-03-21 18:03:44
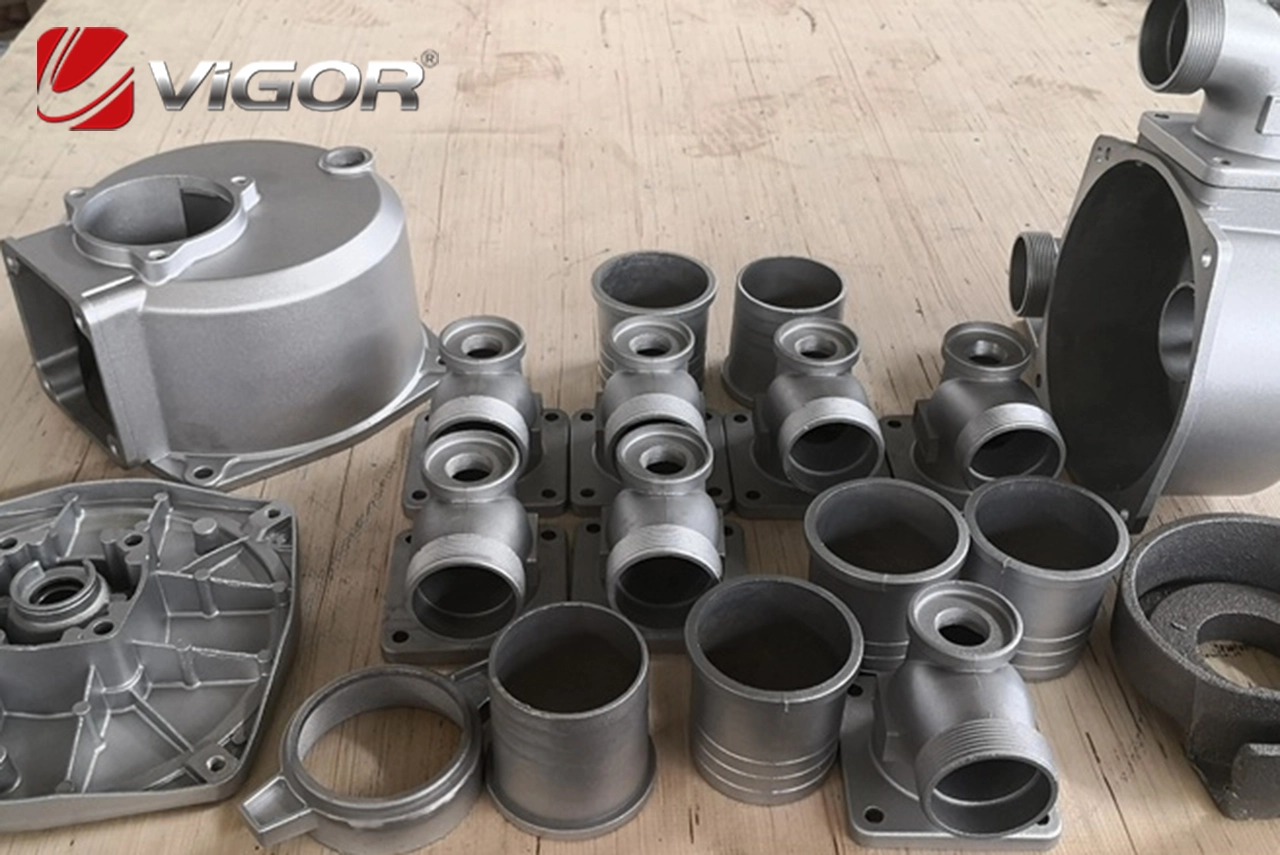
Mold design is a crucial step in the die-casting process, directly influencing the quality of the castings and production efficiency. It requires comprehensive consideration of the casting's shape, size, functional requirements, as well as the fluidity and solidification characteristics of the alloy.
Mold material selection: Commonly used mold materials include steel and aluminum alloys, among which H13 steel is widely employed due to its excellent thermal stability and wear resistance. The choice of mold material should be based on the production volume of the castings, the type of alloy, and cost-benefit analysis.
2025-03-19 18:23:02
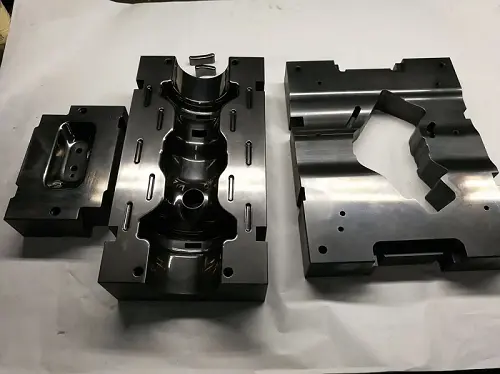
The functions and characteristics of the inner cavity coating of molds and various coatings are as follows:
2025-03-19 18:22:07
Cracks in castings are common problems in the casting manufacturing process. The causes are complex and diverse, mainly including internal defects in the casting, temperature stress, pressure stress, unreasonable casting design, and improper cooling measures.
2025-03-19 18:18:23
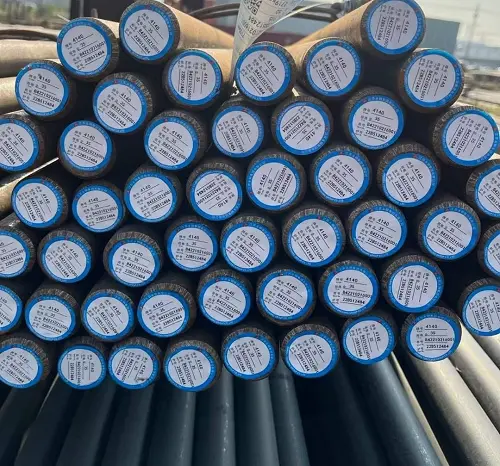
42CrMo4 + QT steel, material No. 1.7225 (Standard EN 10083/3 // ISO 683/1 3) is a European standard alloy steel, usually delivered in tempered and quenched states. It possesses high strength, high toughness, excellent quenching performance, temper brittleness, high fatigue limit, good impact resistance after quenching and tempering, as well as low-temperature impact toughness. This steel is suitable for manufacturing medium and large-sized plastic molds, transmission gears, rear axles, bearing connecting rods, spring lock washers and deep oil well drill pipe joints that require certain strength and toughness.
2025-03-19 15:03:42
We know that the three key elements of gear tooth profile modification design are: modification amount, modification curve and modification height. Then, how are the three variables determined during tooth profile modification design? And what design considerations are there during tooth profile modification design?
2025-03-18 16:41:37
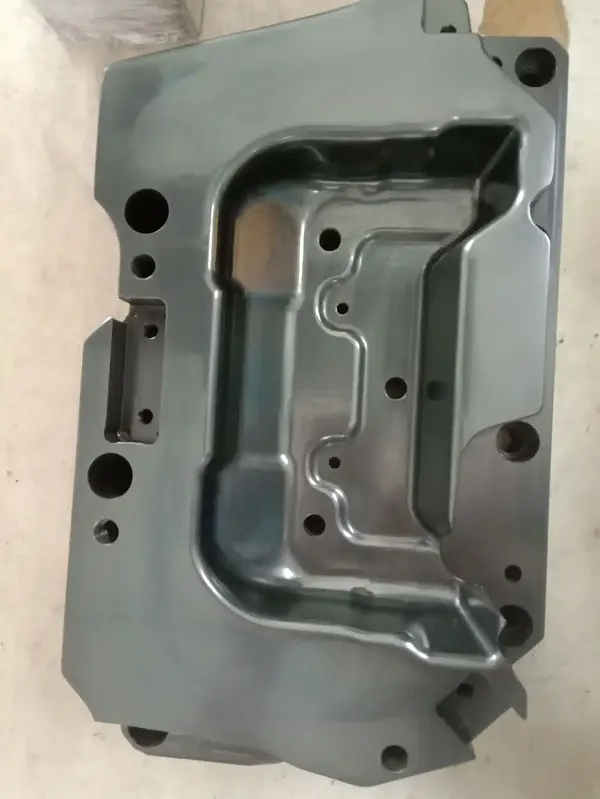
Titanium plating on molds is a new type of surface treatment technology for molds that integrates materials science, physics, electronics, chemistry, and social environmental science. This technology is applied in metal processing, manufacturing processing, and product performance, aiming to promote the rapid development of modern cutting and manufacturing industries.
2025-03-18 16:37:04
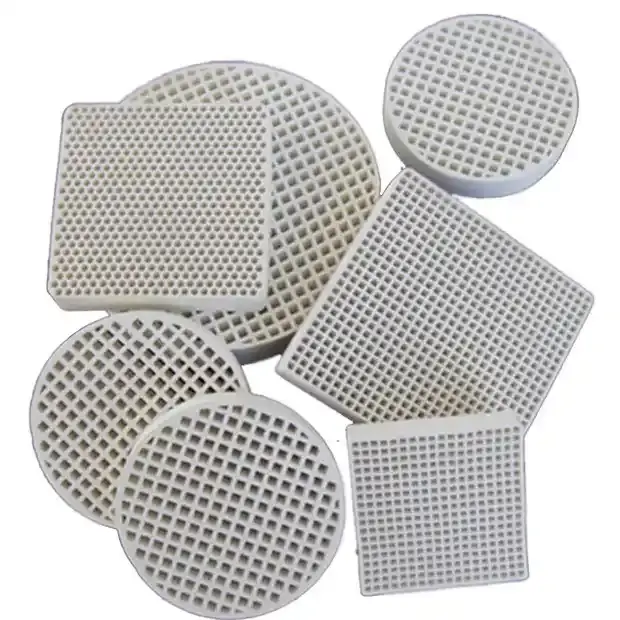
The working principle is to make the turbulent and agitated molten metal become stable, uniform and clean after passing through the honeycomb holes of the foam ceramic. The unique honeycomb structure can adsorb some small particles on its surface, removing impurities that cause surface problems of the product and reduce the strength of the casting, such as some non-metallic particles, slag, refractory material fragments, etc. The stable laminar flow of the molten metal better fills the mold, effectively removing non-metallic inclusions in the molten metal, improving the microstructure and mechanical properties of the casting, and producing high-quality standard castings, reducing the wear of tools during casting processing.
2025-03-18 16:31:56
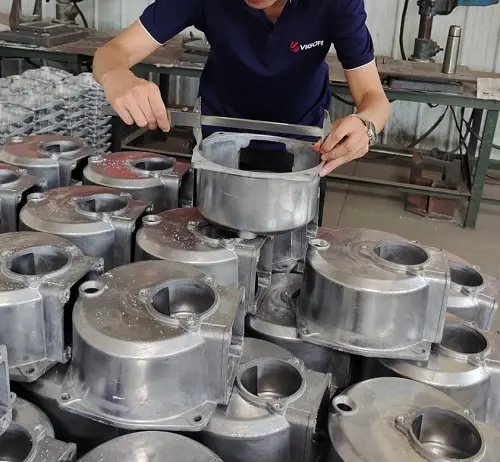
Metal die casting, often referred to simply as die casting, is a casting process that involves injecting molten metal at high pressure into a precision metal mold cavity and allowing it to solidify under pressure to form a casting. This process, characterized by its high speed and pressure, enables the production of metal parts with complex shapes and thin cross-sections. The history of die casting can be traced back to the 19th century. In 1838, the first die casting equipment was invented for manufacturing molds for letterpress printing. The first patent related to die casting was issued in 1849 for a small manual machine used to produce lead type for printing presses. In 1885, Otto Mergenthaler invented the Linotype typesetting machine, which could cast an entire line of text as a single piece of type, revolutionizing the printing industry. At the beginning of the 20th century, with the rapid development of industry, die casting technology began to be widely used in the automotive, aerospace, and other industrial sectors for the production of various complex metal parts.
2025-03-18 16:29:18
The densities of different casting materials vary. Here are some density data of common casting materials:
2025-03-17 17:39:42
302