
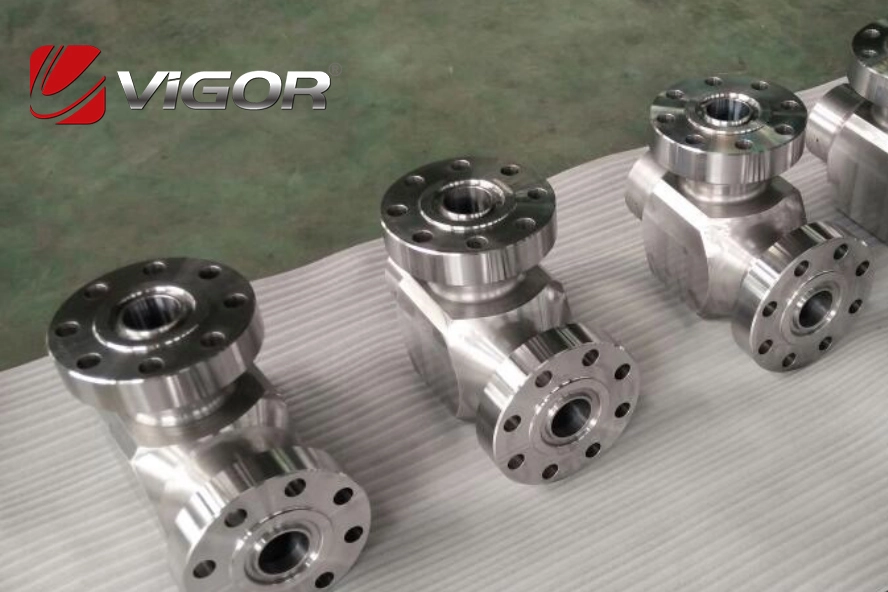
In the extreme working conditions of chemical engineering, nuclear power and other fields, Incoloy 800HT has become a star material in the pressure vessel industry due to its "high-temperature resistance, corrosion resistance and high strength" trinity performance. Today, we will deeply analyze the "genetic code" and practical capabilities of this alloy!
2025-05-27 17:01:19
Recrystallization refers to the crystallization process of solid metals and alloys without phase transformation. It is the process of softening metals or alloys that have undergone work hardening without phase transformation.
2025-05-27 16:43:18
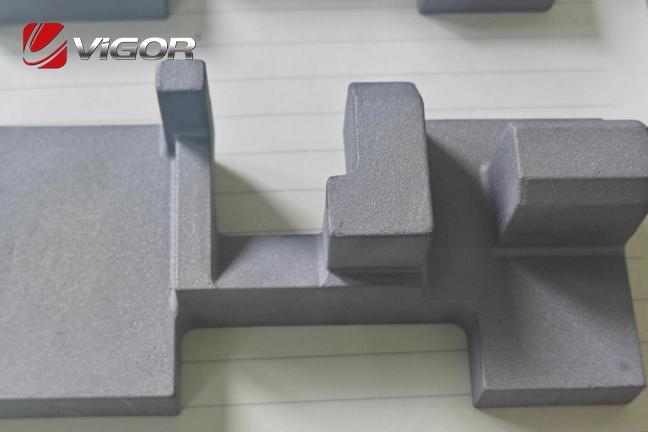
During the solution treatment of 17-4PH martensitic stainless steel, elements such as copper and niobium dissolve into the austenite grains. After cooling, supersaturated copper and niobium martensite is obtained, achieving the first strengthening. Then, during the aging process, the supersaturated copper and niobium elements in the grains precipitate, which provides the second strengthening for the matrix. This is the main strengthening method for 17-4PH steel.
2025-05-27 16:29:34
17-4PH stainless steel (ASTM) is a martensitic precipitation-hardening stainless steel, equivalent to the national standard 05Cr17Ni4Cu4Nb. This type of stainless steel has a low carbon content, high Ni and Cr content, good weldability and excellent corrosion resistance. At the same time, the content of alloying elements such as Cu and Nb in this steel is also relatively high. These alloying elements can precipitate and age hardening phases such as ε-Cu, NbC, and M23C6 during heat treatment, endowing the material with high strength and hardness. Due to these advantages, 17-4PH martensitic precipitation-hardening stainless steel is widely used in aerospace, chemical, and nuclear industries, among others. The mechanical properties of precipitation-hardening stainless steel are significantly related to the heat treatment state. The conventional heat treatment process for 17-4PH martensitic precipitation-hardening stainless steel is solution treatment + aging treatment, which improves strength, hardness, and corrosion resistance by adjusting the microstructure and controlling the precipitated phases. Currently, the research on the heat treatment process of 17-4PH stainless steel is quite mature. This article summarizes and briefly describes its performance and mechanism under different heat treatment processes.
2025-05-21 16:48:32
After quenching and tempering treatment, 40Cr steel has excellent comprehensive mechanical properties, is moderately priced, and is easy to process. Currently, it is one of the most widely used steel grades in the machinery manufacturing industry. China Vigor is actively and deeply involved in the deep processing sites of its customers to understand their product process flows; by analyzing abnormal samples, it identifies the fundamental causes of surface cracks in 40Cr forgings and proposes solutions. On the one hand, it guides customers to improve their production processes and maintains a good relationship with them; on the other hand, it also understands the terminal uses of the products and promptly adjusts the production processes of 40Cr continuous casting billets (or rolled materials) to produce products that meet market demands.
2025-05-21 16:44:39
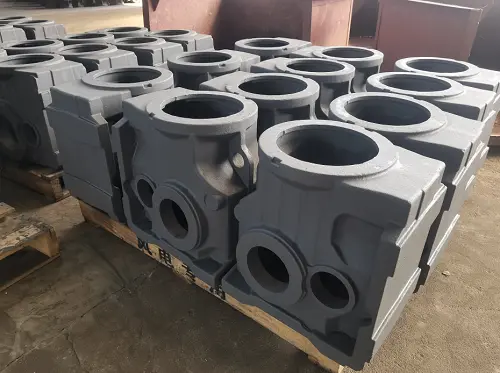
During the manufacturing process of ductile iron, there are a series of trace elements that interfere with the spheroidization process. Although the mass fraction of these elements in ductile iron is only a few parts per ten thousand or a few parts per hundred thousand, they can significantly affect the spheroidization effect. This interference is closely related to the magnesium content in the melt and the cooling rate, and the effects of various interfering elements are superimposed.
2025-05-21 16:25:53
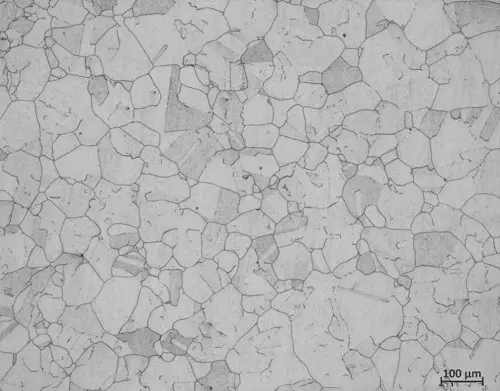
Austenitic stainless steel has a main body of austenitic structure (γ phase) with a face-centered cubic (fcc) lattice. Common types include 304, 316, etc. It is non-magnetic and is mainly strengthened through cold working.
2025-05-20 16:14:38
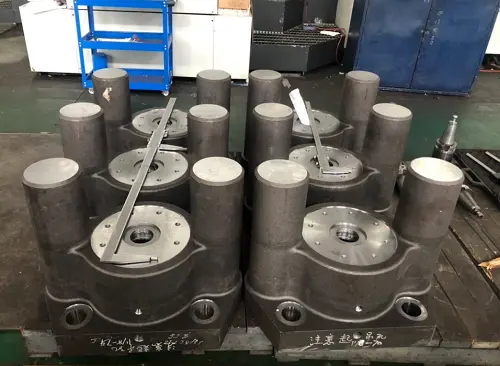
During the manufacturing process of ductile iron, there are a series of trace elements that interfere with the spheroidization process. Although the mass fraction of these elements in ductile iron is only a few parts per ten thousand or a few parts per hundred thousand, they can significantly affect the spheroidization effect. This interference is closely related to the magnesium content in the melt and the cooling rate, and the effects of various interfering elements are superimposed.
2025-05-20 16:07:38
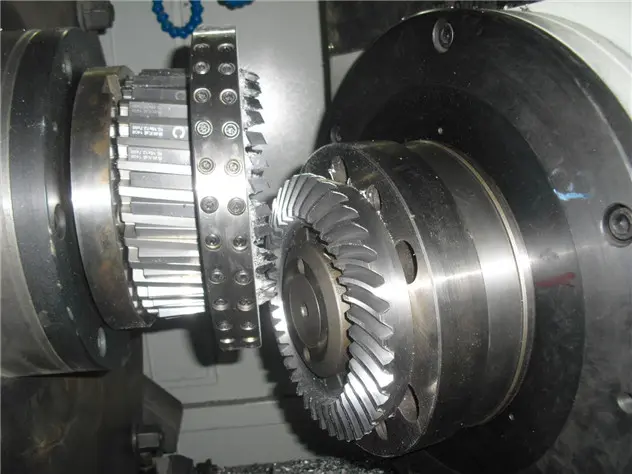
Gears are commonly used components in mechanical design. By the cooperation of two gears, power can be transmitted. The combination of large and small gears can change the output speed and torque, while the cooperation of bevel gears can change the direction of power output. There are various forms of gear tooth profiles, among which involute tooth profile is the most common. The common processing methods of involute tooth profile are divided into two major categories: forming method and generating method. Here, we will not explain them in detail. Next, we will focus on introducing the common processing methods of gears.
2025-05-20 16:02:28
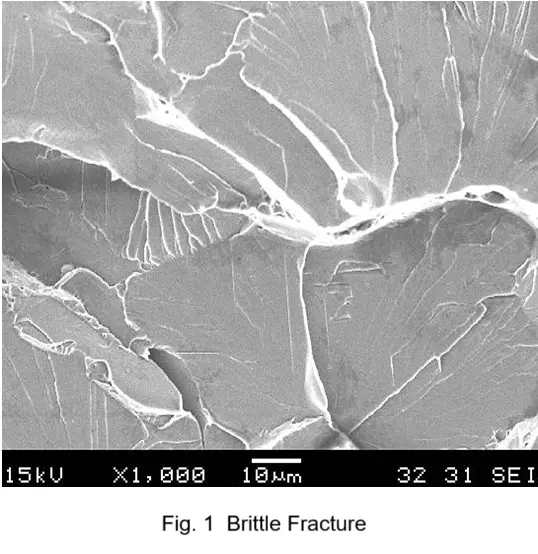
Fracture surface analysis holds a particularly important position in fracture failure analysis, as various information related to fracture is recorded on the fracture surface. Through the analysis of the fracture surface, the cause of fracture and its influencing factors can be identified. Microscopic fracture surface analysis mainly utilizes instruments such as metallographic microscopes, scanning electron microscopes (SEM), transmission electron microscopes (TEM), and electron probe microanalyzers (EPMA) to study the microscopic process of fracture, the fracture mechanism, and analyze various influencing factors leading to failure.
2025-05-19 12:06:23
_1747627357353.webp)
During the manufacturing process of ductile iron, there are a series of trace elements that interfere with the spheroidization process. Although the mass fraction of these elements in ductile iron is only a few parts per ten thousand or a few parts per hundred thousand, they can significantly affect the spheroidization effect. This interference is closely related to the magnesium content in the melt and the cooling rate, and the effects of various interfering elements are superimposed.
2025-05-19 12:03:15

The discontinuity of metallic materials refers to the non-uniformity and sudden changes in their internal structure, composition or performance. In the study of failure analysis cases, it is found that many failures are caused by the discontinuity of materials.
The discontinuity of structure is mainly reflected in two aspects: internal defects and the inhomogeneity of the organization.
2025-05-19 12:01:51
302