
This paper briefly describes the structural features, technical requirements and manufacturing difficulties of heavy ductile iron castings. It elaborates on the casting methods, gating system design methods and manufacturing methods of this type of castings. The process characteristics, production advantages and application scope of resin sand solid mold casting are introduced. Through strict process control, selection of appropriate raw materials, proper spheroidizing and inoculation treatment processes, and special pretreatment techniques during the production process, high-quality large ductile iron castings can be produced. This can provide technical references for the solid mold casting process of similar heavy castings.
2025-08-27 15:32:17
Pitting refers to small and shallow pits that appear in the contact area of gear teeth surfaces. These pits are usually formed due to local material spalling. At the beginning of pitting, they are generally tiny spots. With the passage of time and the continuous action of load, these spots gradually expand, deepen, and connect with each other, forming larger areas of spalling, which seriously affects the working performance of gears.
2025-08-27 15:20:42
To correctly consider feeding and gating, it is necessary to understand alloy solidification. The solidification mechanisms of different alloys can vary significantly. Therefore, the methods for producing dense and defect-free castings also differ. This article considers some basic factors that influence the solidification pattern and discusses how these factors affect the design methods of risers and gates.
2025-08-27 15:16:59
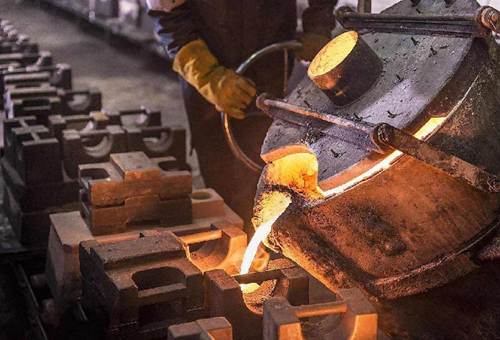
The gating system of castings is mainly responsible for transferring clean and slag-free molten steel from the ladle to the mold cavity without causing secondary oxidation or gas absorption. To some extent, all alloys are affected by slag formation, and some, such as aluminum-based and copper-based alloys, are particularly susceptible.
2025-08-27 15:13:13
To ensure stable product quality during batch manufacturing, this model is processed and controlled with full numerical control for high-precision machining, further enhancing the accuracy and stability of the model's dimensions. The model is also subjected to three-dimensional data detection to comprehensively inspect all its dimensions and shapes, ensuring its quality and precision. This is crucial for batch manufacturing of castings and can effectively prevent casting quality issues caused by model errors. The three-dimensional model is illustrated in Figure 9, and the three-dimensional detection data is shown in Figure 10.
2025-08-27 15:06:10
After analyzing the part structure, material properties, technical requirements and casting process difficulties of the CB2 main steam valve regulating valve shell casting, as well as considering potential casting quality issues, through the research on the cause of valve shell cracks, solidification zone feeding and the setting of cold iron in the solidification end zone, the common defects such as porosity and cracks in the casting process were effectively solved. A reasonable and practical casting process plan was developed, and the control of the manufacturing process was strengthened, improving the stability of the process and operation. After production verification, the overall quality of the valve shell was good, meeting the standard requirements, and the batch manufacturing of the CB2 main steam valve regulating valve shell was successfully achieved.
2025-08-27 15:04:18
What kinds of steel are used for gear nitriding? And some microstructure characteristics of commonly used steels. Understanding the microstructure characteristics can help to bring out the good performance of gears in use, and at the same time optimize the gear manufacturing process, which is conducive to improving the service life of gears.
2025-08-13 17:48:37
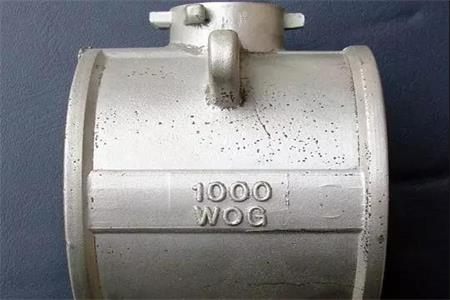
(1) Characteristics: There are numerous small pitted holes on the surface of the casting, with diameters ranging from 0.3 to 0.8 mm and depths of 0.3 to 0.5 mm. This defect often occurs on alloy steel castings with low carbon content and w(Cr) ranging from 5% to 18%. Before cleaning, the shallow pits are filled with slag-like substances.
(2) Causes: The pitting is mainly caused by chemical reactions between metal oxides and oxides in the shell material.
(3) Locations: On the local or entire surface of the casting, with more occurrences in thin-walled areas.
(4) Illustration: See Figure 1.
2025-08-13 17:45:14
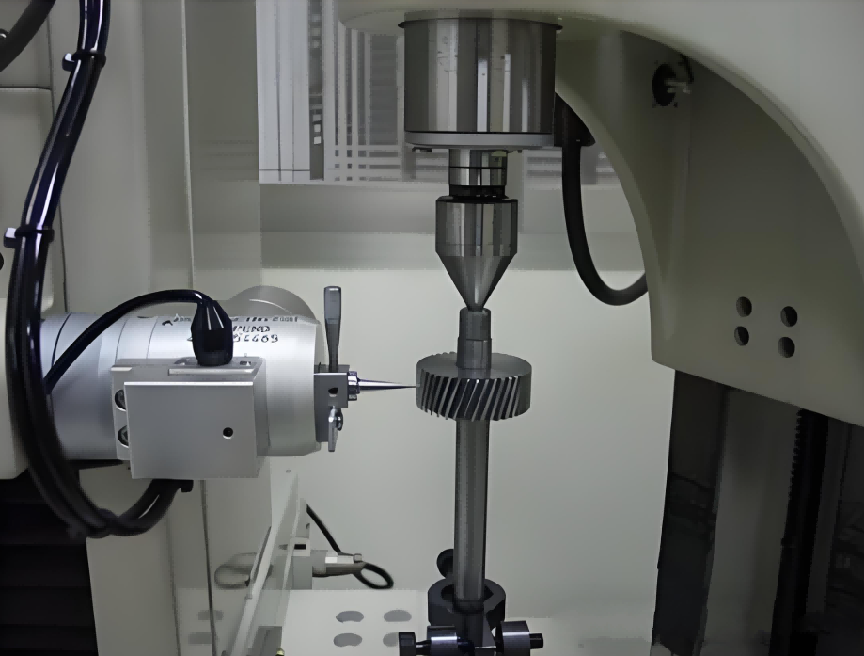
This article elaborately describes the meaning of gear accuracy, its evaluation system and control methods, and conducts a detailed analysis of the mainstream international accuracy standards such as ISO, AGMA and DIN. It also explores the accuracy control strategies and detection technologies in the gear manufacturing process, providing theoretical guidance and technical references for gear design and manufacturing.
2025-08-07 17:03:30
Gears are the core components of mechanical transmission systems, and their reliability directly affects the operational life and safety of equipment. However, under high-speed, heavy-load or harsh working conditions, gears often fail due to various reasons, such as fracture, leading to equipment downtime or even safety accidents. Pitting is also a common failure mode of gears, which can reduce transmission efficiency, increase noise, and even cause complete gear failure.
2025-08-07 16:53:42
Copper has excellent electrical conductivity, thermal conductivity, corrosion resistance, ductility and certain strength. Adding various alloy elements to copper can improve its corrosion resistance, strength and improve its machinability.
2025-08-07 16:46:54
302